- Ruhr-Universität Bochum
Direct control of temporally and spatially resolved flow fields in hydraulic fluid machinery using the example of cavitation in pumps
In numerous industries and applications, pumps are crucial for fluid transport. They are used in building technology, water and wastewater management, energy production, shipping, agriculture, and industrial process plants. Despite their widespread use, these pumps often do not operate at their most energy-efficient point, leading to several disadvantages. Suboptimal pump operation can significantly increase energy consumption, thereby raising operating costs and environmental impact. Specifically, the formation of cavitation bubbles causes substantial damage to pump components, increasing maintenance and repair costs, extending downtime, and ultimately shortening the pump’s lifespan.
Based on results from a previous research project (see Real-time Capable Digital Twins of Centrifugal Pumps), this project, funded by the Federal Ministry for Economic Affairs and Climate Action (BMWK) under the Industrial Collective Research (IGF) program, aims to develop an innovative control strategy for centrifugal pumps based on real-time capable digital twins. The goal is to enable optimal operation through real-time, flow-field-resolved control that prevents cavitation formation in pumps.
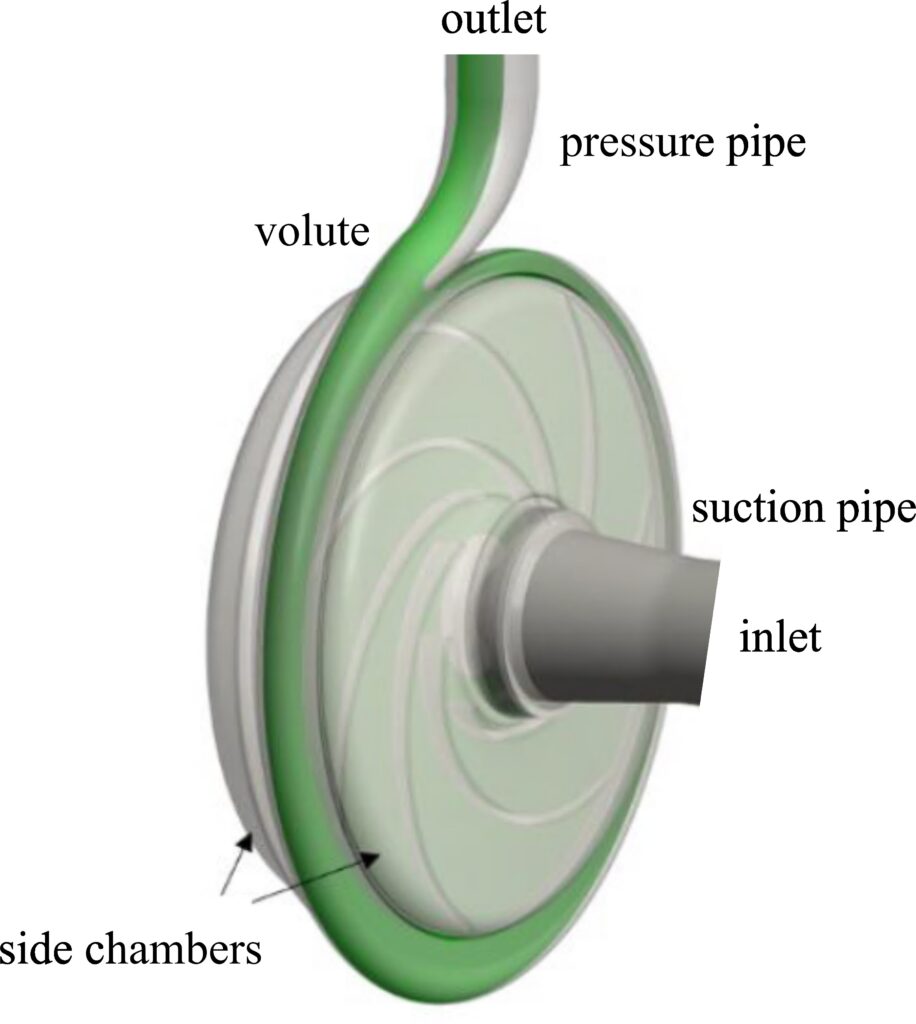
3D model of a centrifugal pump.
The development of such control systems requires detailed knowledge of the spatially and temporally resolved, as well as parameter-dependent, volumetric flows and pressure fields within the pump. However, due to the complex flow conditions and limited accessibility of the pump for direct measurements, obtaining this information is challenging. Therefore, innovative methods must be developed to overcome this challenge.
In the project, highly resolved flow simulation models from computational fluid dynamics (CFD) will be reduced to parametric reduced order models using proper orthogonal decomposition and nonlinear interpolation methods, making them suitable for use on microcontrollers in pumps.
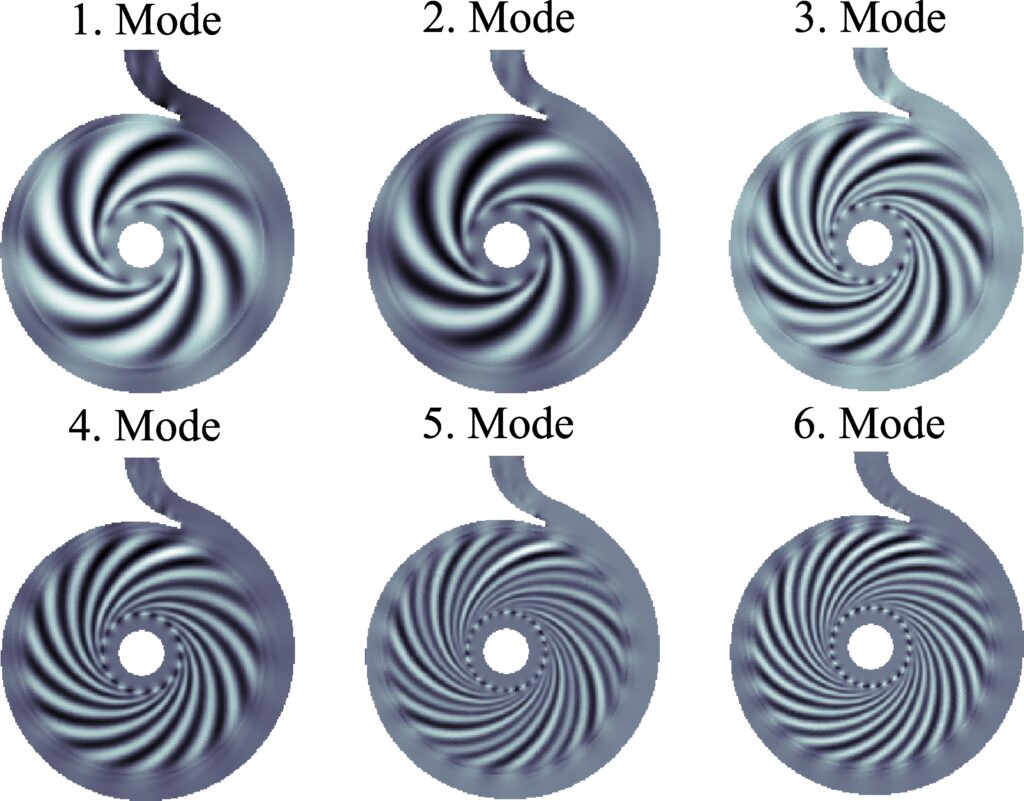
The first six basis vectors (also called modes) of a total of 16 basis vectors for the pressure in an axial section of a centrifugal pump.
This approach reduces the complexity of flow models while maintaining accuracy. Combined with a few measurements at optimally placed locations, the parametric reduced order models serve as the basis for estimating flow fields and pressure distributions. By integrating measurement data with model-based estimates, known as soft sensors, comprehensive flow parameters, including the entire flow field, can be determined with high accuracy. This requires only a small number of measurements, approximately 10 pressure measurements at optimally selected and accessible locations. These measurement points are identified through model-based observability analyses, which provide insights into the amount of available local information about the flow field.
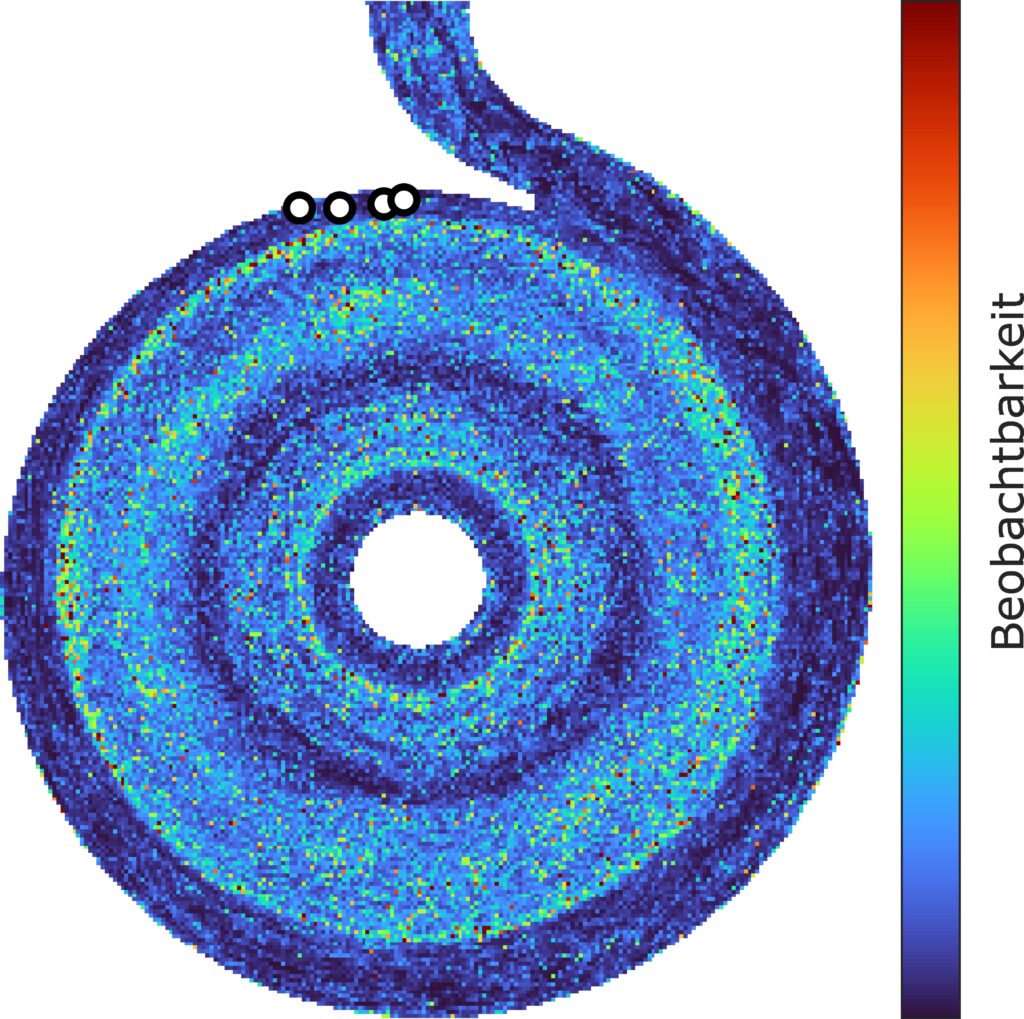
Heatmap of observability (measure of the optimality of the measurement location) in the axial section of the centrifugal pump. The four circles indicate the first four optimal measurement locations.
Integral quantities for cavitation detection are derived from the determined flows. Based on the results of the flow field estimation and cavitation detection, a real-time control strategy is designed to optimally adjust the pump’s operating point, preventing cavitation formation while optimizing energy efficiency.
The technical implementation of the project includes the development of two-phase cavitating flow simulations and parametric reduced order models, the implementation of soft sensors, the integration of cavitation detection, and the development of the flow-field-resolved control strategy. Finally, the method will be validated on a hardware-in-the-loop test bench.
This research project is conducted in close collaboration with the Chair of Hydraulic Fluid Machinery (HSM) at Ruhr University Bochum.
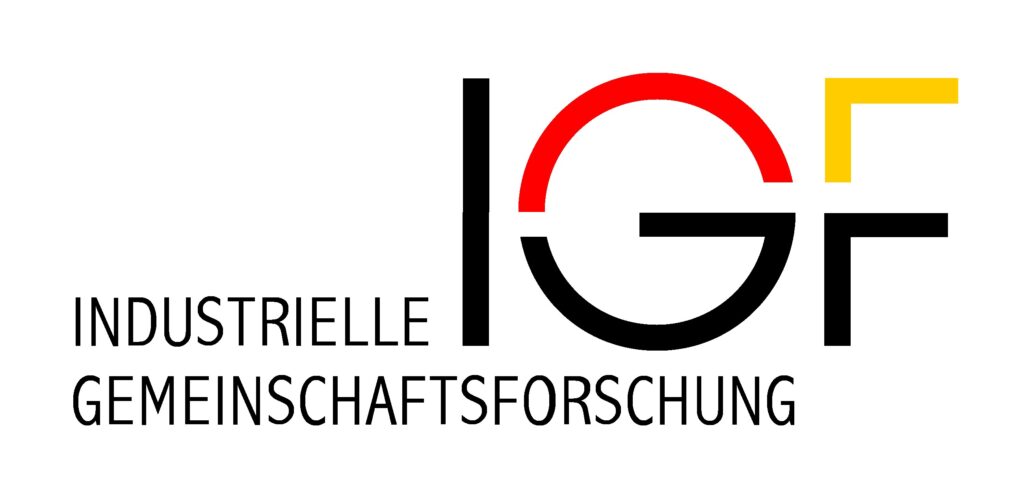
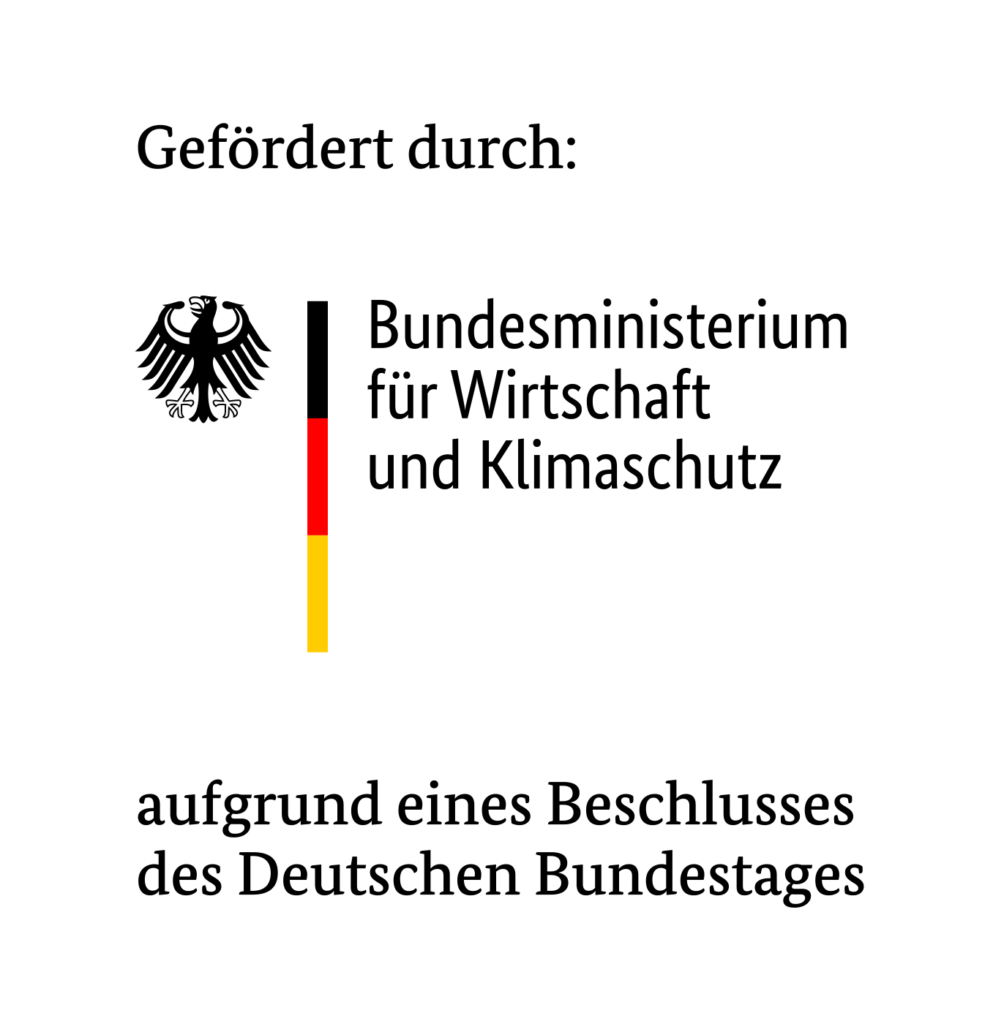