- Ruhr-Universität Bochum
Das pulverbasierte Laserauftragschweißen (engl. Laser Metal Deposition, LMD) ist ein vielseitiges Verfahren der additiven Fertigung, das insbesondere für die Beschichtung von Bauteilen mit funktionalen oder verschleißfesten Materialien eingesetzt wird. Dabei wird metallisches Pulver gezielt in einen fokussierten Laserstrahl eingebracht, aufgeschmolzen und sowohl schichtweise als auch bahnweise auf das Bauteil aufgetragen. So entstehen aus nebeneinander überlappenden Schweißbahnen fest haftende Schichten mit spezifischen Eigenschaften wie beispielsweise erhöhter Korrosions- oder Verschleißbeständigkeit, die die Lebensdauer und Leistungsfähigkeit von Komponenten signifikant erhöhen können. Neben der Beschichtung erlaubt das Verfahren auch den vollständigen schichtweisen Aufbau komplexer Geometrien von Grund auf und die Reparatur beschädigter Bauteile.
Im Vergleich zu konventionellen Fertigungsverfahren wie Fräsen oder Gießen bietet das Laserauftragschweißen mehrere Vorteile: Es ermöglicht einen gezielten Materialauftrag nur dort, wo er funktional notwendig ist, reduziert Materialverluste und erlaubt eine hohe geometrische Flexibilität. Besonders bei der Nachbearbeitung oder Aufwertung bestehender Komponenten, etwa durch Hartauftragsschichten oder lokale Verstärkungen, stellt das Verfahren eine wirtschaftliche und ressourcenschonende Alternative zur Neufertigung dar.
Bei bestehenden Laserauftragschweißanlagen ist die Bahnbreite auf 4 mm beschränkt, sodass zur Fertigung oder Beschichtung von großvolumigen Bauteilen eine Vielzahl von Bahnen nebeneinander aufgetragen werden muss. Aufgrund dieser Tatsache leidet die Prozesseffizienz und die Wahrscheinlichkeit für Fertigungsfehler erhöht sich.
Genau hier setzt das Projekt „BreitbahnDED“ an: Gemeinsam mit Projektpartnern wird ein neuartiger Prototyp einer CNC-basierten Laserauftragschweißanlage entwickelt. Das Ziel des neuartigen Konzepts ist es, im Vergleich zu konventionellen Anlagen breite, gleichmäßig hohe Schweißbahnen bei annähernd gleichem Energieeinsatz zu generieren, sodass die Effizienz des Prozesses erhöht und gleichzeitig die Wahrscheinlichkeit für Fehler minimiert wird.
Ein zentraler Bestandteil der innovativen Anlage ist der neuartige Bearbeitungskopf, der die präzise Führung und Fokussierung des Laserstrahls auf das Werkstück gewährleistet. Der Laserstrahl wird innerhalb des Bearbeitungskopfes durch eine rotierende Multispotoptik geleitet, welche aus diffraktiven optischen Elementen (DOEs) besteht. Die Multispotoptik übernimmt zwei Aufgaben: Erstens wird der Laserstrahl auf mehrere Teilstrahlen aufgeteilt und zweitens entstehen durch die hochfrequente Rotation gemittelt über eine Umdrehung mehrere Ringe auf der Werkstückoberfläche. Folglich wird die Energie des Lasers flächiger und ökonomischer verteilt. Die optimierte Energieeinkopplung führt zur Erzeugung eines großflächigen Schmelzbads mit einer homogeneren Temperaturverteilung, das die Herstellung porenarmer, breiter Bahnen mit definierter Schichthöhe erlaubt (vgl. Abb. 1).
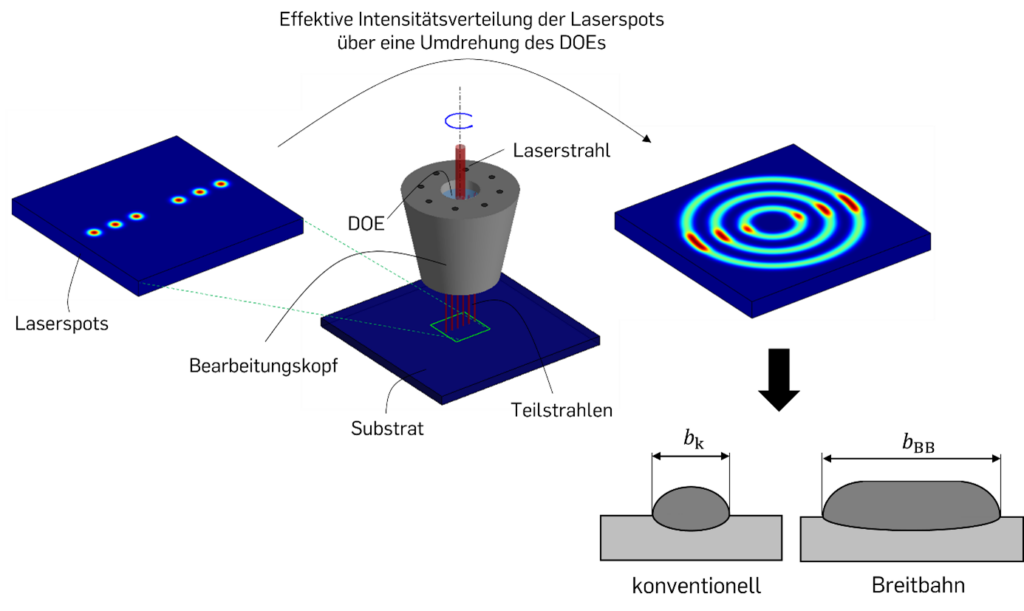
Der Aufgabenbereich des LRS umfasst die Entwicklung und Implementierung einer Regelungsstrategie für den neuen Prozess. Die durch die Rotation der Teilstrahlen entstehende Energieverteilung führt zu einer komplexen Temperaturverteilung, die sich mithilfe numerischer Simulationsverfahren umfassend beschreiben lässt. Für eine echtzeitfähige Regelung auf einem eingebetteten System wird das von den Projektpartnern entwickelte Modell der Temperaturverteilung durch projektionsbasierte und KI-gestützte Modellreduktionsverfahren gezielt so vereinfacht, dass eine zeitkritische Lösung innerhalb des Regelungsalgorithmus möglich wird. Die zentrale Herausforderung besteht dabei in der simultanen Berücksichtigung von Rechenzeiteffizienz, Generalisierbarkeit über verschiedene Legierungen hinweg sowie der Parametrisierung des reduzierten Modells in den relevanten Eingangsgrößen. Das reduzierte Modell bildet die Grundlage für die anschließende Regelung der räumlichen Temperaturverteilung im dynamischen Prozessverlauf. Der zu entwickelnde Regler ist auf zeitlich und räumlich hochaufgelöste, zuverlässige Messdaten angewiesen, um die Regelgüte sicherzustellen. Zu diesem Zweck wird am LRS eine Sensorfusion bestehend aus mehreren CMOS-Kameras und einem Pyrometer realisiert, um das Schmelzbad sowie den angrenzenden Bereich kontinuierlich zu überwachen.
Ein weiterer Schwerpunkt liegt auf der Entwicklung einer Schicht-zu-Schicht-Regelung mit dem Ziel, eine endkonturnahe Fertigung zu ermöglichen. Hierbei sollen geometrische Abweichungen vorangegangener Schichten durch gezielte Korrekturen in nachfolgenden Schichten kompensiert werden. Dies erfordert eine dynamische Anpassung des zuvor generierten G-Codes in Echtzeit (vgl. Abb. 2). Um eine vorausschauende, optimal abgestimmte Regelgüte zu erreichen, werden mehrere Stellgrößen gleichzeitig berücksichtigt. Ergänzend kommen systemtheoretische Methoden zum Einsatz, um die Konvergenz der finalen Bauteilhöhe theoretisch abzusichern.
Projektpartner:
- – Lehrstuhl für Laseranwendungstechnik (LAT), Ruhr-Universität Bochum
- – LMB Automation GmbH, Iserlohn
- – Kamp und Kötter GmbH, Bochum
- – ThinkIng – Additive Technology GmbH/exafuse, Bochum
Das Forschungsprojekt wird im Rahmen des Innovationswettbewerb Industrie.IN.NRW durch das EFRE/JTF-Programm NRW 2021-2027 gefördert.
Der LRS dankt den Projektträgern EFRE und dem Land NRW für die Förderung des Forschungsprojektes.
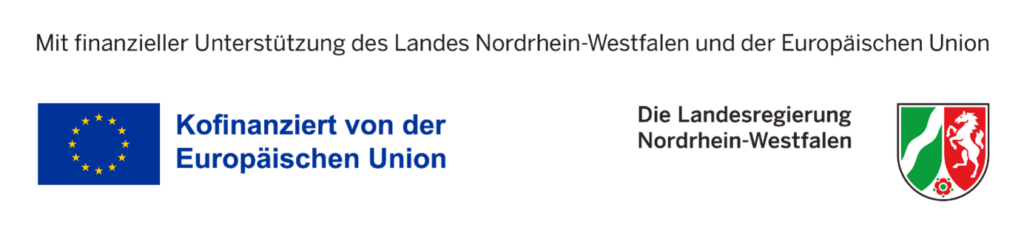